This article discusses about the crankshaft deflection and bearing clearance measurement in details. Both of the process is crucial for the any engine onboard. But here we will focus our approach towards the main engine only. But for crankshaft deflection related to generators is more or less same.
Read this interesting article: Main engine crankcase inspection-What to check
Crankshaft Deflection
The question always arises as why we are something. Well the simple reason here for crankshaft deflection is that it gives us rough estimate as how good our main bearings are and how much wear down have taken place. And together with this, you will have another activity called as bearing clearance. The deflections are measured at one end of the crank web, and moving the crankshaft at different positions which we will discuss later in this article.
Crankshaft Deflection- When they are taken
Following conditions might be there when you have to measure the crankshaft deflection as well as the bearing clearance too.
1) Planned maintenance activity
2) Any overhaul related to the bearing
3) During any change of propeller- before and after
4) During damage to ship like grounding etc.
Crankshaft Deflection and Bearing Clearance-How to Do
Following is the standard procedure to do the above activity. Proper planning of man power and time to be done before starting this job. For example it will need at least two people to do the whole activity and time duration of 3 hours if you have 8 cylinder engines. Following points to be followed for carrying out this job:
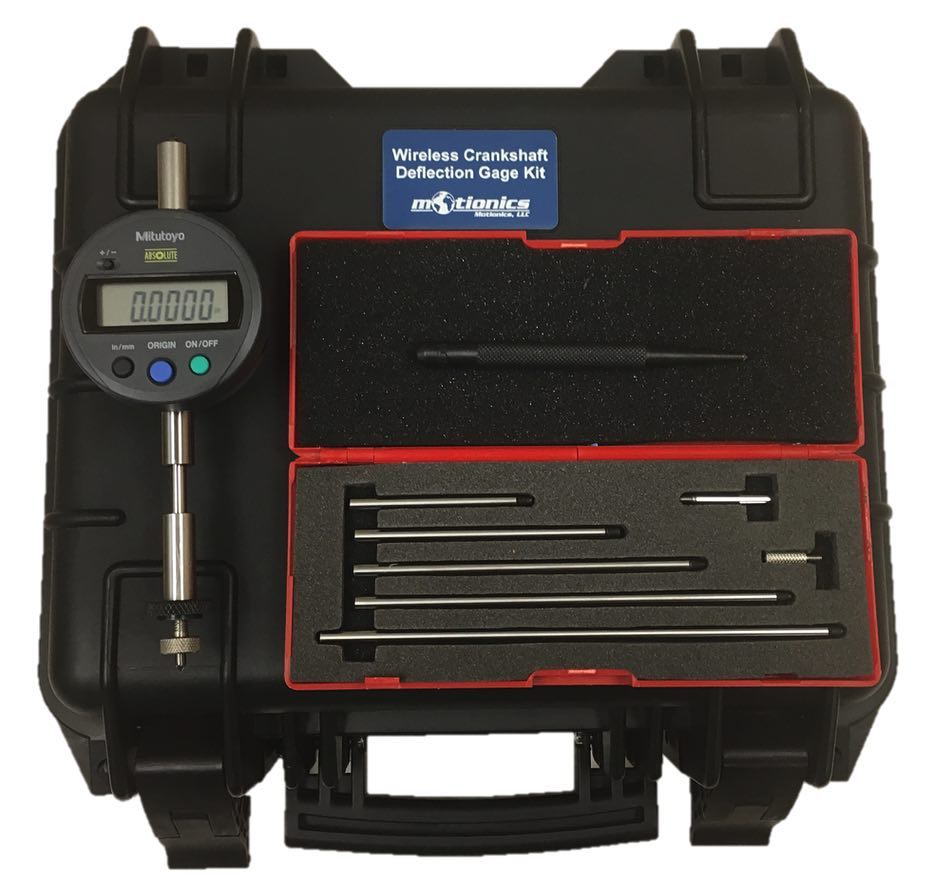
1) Apply for immobilization for the port in which you have to carry out the activity.
2) Prepare the feeler gauges and deflection gauge prior to the job.
3) Printout the template form for writing the values obtained during the deflections and bearing measurement.
4) It is good practice to finish the deflection in one go for all the units and then start the bearing Clarence measurement. This saves time.
5) Make work permit and PPE as per the scope of the job needs to be done.
6) When finished with engine, engage the running gear and switch of the lubrication pump (after 1 hour when stopped).
7) Ask the deck officer for the draft forward and aft.
8) Open the crankcase door and ventilate the space properly.
9) Now note down the firing sequence and start with the first unit that comes in the sequence.
10) One person has to go down and put the deflection gauge in the slot given on the crank web. Make sure that it reads zero. Below image shows the positions and place where you have to put the deflection gauge.
Note: The engine to be turned in the direction as per the instructions in the manual. Also the top position will have two readings because the crankpin comes in the way. So first move the crankshaft in opposite direction and take one reading. Then turn in regular direction, and 2nd reading will be at the end of the revolution. Mean of these two readings will give you valve of top part.
11) It is easy to put dial gauge when crank webs are at the bottom, which means unit is at TDC. Make sure it reads zero. And once you start turning for next reading. Don’t stop in between.
12) So looking at the above image, you will put gauge when webs are at bottom. Then turn shaft in anticlockwise direction till red mark.
13) Now measure the value. Now turn the shaft in clockwise direction and take all the valve mentioned at the location above.
Main Bearing Clearance Measurement
After you are done with the deflections, you are now required to measure the clearances. Here is the step wise guide for it.
1) For main bearing clearance measurement, you can use the depth gauge or telescopic feeler gauge. The measurement is made for the distance between upper shell and the crankshaft. If you are using feeler gauge then, move the webs in horizontal position for easy measurement.
2) For measurement of crankpin bearing clearance or bottom end bearing. Move the unit to BDC and then using feeler gauge, measure the clearance.
3) For Measure of the crosshead bearing clearance measurement, turn the unit to BDC. And using the feeler gauge, check both forward and after part clearance of the bearing.
4) Match the recorded values with the one given by the manufacturer. Over the time values should differ.
So this was all from this article on crankshaft deflection and main bearing clearance.